
The manufacturing industry is a thriving area that keeps finding applications for upcoming technologies in its various processes. Manual methods that relied solely on a keen eye are now the core of some leading manufacturing software. Inventory management is one of the most practical applications that maximise the capability of existing programs, diving into the nuts and bolts of a manufacturing operation.
Spare parts inventory management is an additional stock control challenge faced by manufacturers.
Taking shortcuts on spare parts inventory management increases your risk of unplanned stoppages.
On the other hand, the lack of a spare component can cause significant production delays. A stockout of certain materials can delay urgent work and contribute to productivity losses. Depending on the contribution of a particular piece of equipment, the unavailability of a part can cause repair delays or even a complete outage. To put things in context, an average automotive manufacturer can lose up to USD 22,000 each minute the production line stops. Imagine how a spare that allows a facility to recover from a breakdown highlights the importance of having stock on hand.
Spare parts inventory management is the balancing act of spending resources on the materials that matter. It minimises the risk of overstocking surplus goods while securing the parts that add value.
Running a tight ship in manufacturing is easier with the right technology.
Your maintenance teams will appreciate an organised spare parts inventory control system.
What is spare parts inventory management?
There are a few terms in spare parts inventory management to unpack. Inventory management talks about the process of bringing in stock for inventory as well as monitoring their usage and movement. Specific aspects of managing inventory include procurement, storage, and utilisation tracking. The terms "spare parts" distinguish the particular type of inventory that requires management. These types of materials refer to components that are essential to the maintenance and continuity of operations. In contrast, examples of other types of materials that may require specialised inventory management strategies are raw materials and finished products.
Why is spare parts inventory management so important?
In 2021, the global demand value in North America for spare parts and consumables relating to maintenance and operations reached over USD 150 billion. This valuation paints a picture of how much companies invest in procuring inventory to sustain the functions of their facilities. However, this also opens the risk of tying up capital in accumulating supply that takes a while to end up in usage. Holding stock can be a problem for several reasons. The most obvious concern is the initial cost of buying a product equivalent roughly to the unit price of a spare. The less noticeable expenses are those associated with acquiring and holding the stock. A company will incur administrative costs from obtaining a quotation to accomplishing a purchase order. Shipping spares will also cost additional fees, especially for components that require special handling. Once a unit arrives at the warehouse, the facility will again have to spend on holding costs to ensure that the stocked units do not deteriorate into an unusable condition. Spare parts inventory management aims to streamline the multiple possible sources of costs to obtain stock. Scheduling the arrival of incoming units, for instance, can reduce the redundant work to go through the entire procurement process for similar products. Moreover, purchasing teams can leverage bulk orders to get a better price. Minimising holding costs is possible by identifying materials that can arrive just in time for scheduled work. Knowing that companies are bound to spend on inventory, a thoughtful inventory management strategy can minimise wastes that are not adding real value to the business.What are the risks of overlooking spare parts inventory management?
Disregarding the ways to manage inventory management can result in extreme scenarios. In a perfect world where everything is free, it might be tempting for one to acquire all the spares in the world to ensure zero waiting time for any maintenance work. Another utopian system might hold no inventory at all, but the lead times for all spares allow to bring them in time before the start of any maintenance activity. Of course, both designs are far from reality and therefore highlight the need for a system to manage stock. Overstocking on parts leaves a company with surplus inventory that does not add immediate value to the business. Apart from holding capital that could have gone to more productive work, remember that it also costs money to keep acquired stock. Typical warehousing costs can charge by volume, and such expenses accumulate as the number of unused spares grows.
What are the key spare parts inventory management best practices?
Regardless of the size of operations or the maturity of a facility, it always helps to revisit their current ways of working to uncover improvement opportunities. Here are some best practices in spare parts inventory management to start.Identify criteria for criticality
While it is true that the success of a facility relies on the collective contribution of various bits and pieces, the reality is that not all parts hold equal value. Having objective criteria for what is considered critical to the business leads to a more systematic approach to carrying appropriate stock levels.Engage with procurement teams
An effective inventory management strategy bridges the gap between the supply and demand sides of the business. Having a platform that communicates the nature of requirements to the procurement teams encourages a more holistic approach to acquiring stock.Consider implementing a hybrid approach
It is common practice for certain suppliers to carry vendor-held stock for a customer. This practice minimises the exposure of a company to holding costs and surplus stock. Companies with the opportunity to implement a hybrid approach that combines conventional and consignment models can achieve quick wins for particular subsets of their inventory.Conduct regular audits
There is no easy way around the evaluation of the effectiveness of any process or equipment. Even when performance indicators show positive results, routine audits enable companies to explore continuous improvement opportunities.Maximise the available technology
Inventory management involves several interacting values that can get very challenging to track manually. Available technology utilizes the power of the internet of things and unprecedented levels of interconnectedness between devices. The capability of modern software goes beyond the historical monitoring of usage and into the world of advanced analytics and forecasting.
Should you run spare parts inventory management in Excel?
Spreadsheets are arguably the most widespread tool that businesses see on a daily basis. Because of the familiarity with how they work and the universal understanding among workers globally, it is easy to fall into the trap of going to spreadsheets for parts inventory management. While a spreadsheet can crunch numbers and calculate complex equations, it offers far less intelligence and autonomy in coming up with actionable decisions. At its core, spreadsheets are the digital counterpart of the proverbial pen and paper, relying a lot on the manual manipulations by the user behind the screen. An evident concern about the dependence on Excel for inventory management is how it ingests data. For the most part, a spreadsheet does not lend itself to automated data inputs and refreshes. The situation worsens when sharing data across individuals or multiple sources as the risk of losing information increases. As the size of the dataset grows, other issues can arise due to the performance limitations of a spreadsheet for substantial amounts of information. Excel does an excellent job of being a versatile tool that is capable of several business-related tasks. However, the same reasons contributing to its strength can become limitations in the modern approach to managing inventory. On the other hand, available tools such as a spare parts inventory management system dedicate their design to the dynamic nature of stock movements.What is a spare parts inventory management system?
A spare parts inventory management system is a specialised type of software that consolidates information about the stock holding of a company. The most valuable feature of an inventory management system is the ability to know the inventory status of spares. For example, by knowing in which warehouse a particular unit exists, companies can evaluate the time it will take to replenish the stock in time for a requirement. It provides valuable insights into the possible causes of stockouts and how to prevent them. A quality inventory management system also enables robust reporting capabilities. This attribute comes in handy when analyzing the individual segments of the end-to-end production process. Areas causing considerable costs in holding or additional handling can highlight areas for improvement. Pieces of information such as vendor performance and supply constraints can also present themselves to provide in-depth visibility across multiple facilities. On top of all the main features of an inventory management system is the readiness for data integration with other available applications and existing processes. The ease of migration, such as incorporating thousands of existing cataloged materials, boosts the usability of these new tools. Integration with other specialized systems also allows for a broadened approach to increase efficiency and eliminate waste in managing stock. For instance, a reliable view of the spare supply can work together with the demand side of operations, such as maintenance requirements.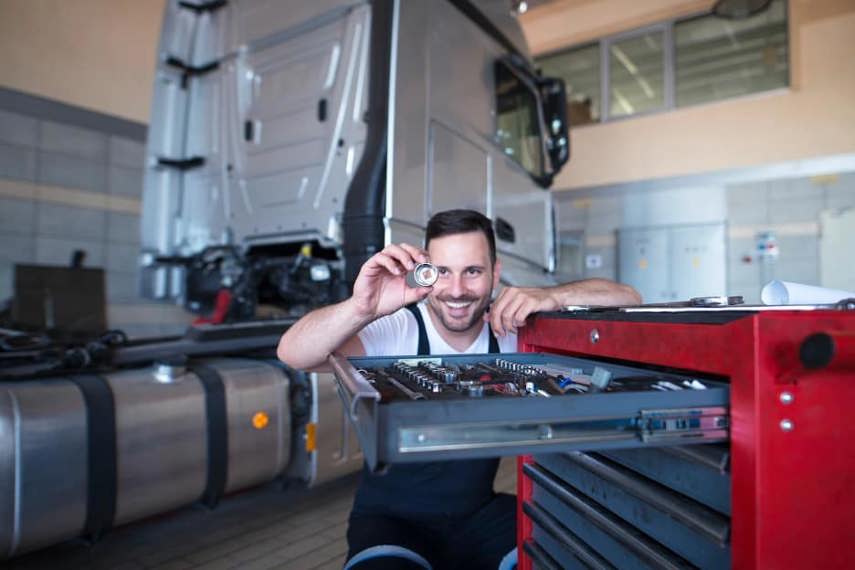