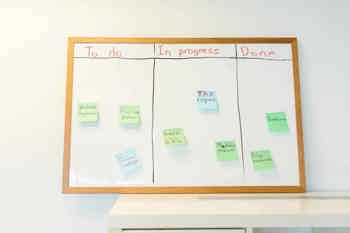
Here we give you eight real-world examples of how businesses use Kanban, a popular lean manufacturing tool that’s helped companies in a huge range of sectors improve efficiency.
Don’t worry if you’re not familiar with what Kanban is – we'll give you the basics first. If you already know what Kanban is and just want the case studies, scroll down!
What is Kanban?
Kanban is a process management tool that visualises the status of each job on a company’s radar, and controls the flow of production from customer requests back to the warehouse.
These days the kanban system is often managed digitally, and provides a very open, transparent way of communicating a project’s status with the wider team, letting everyone see at all times where something is, who was last doing the task, and where it needs to go next.
Kanban came from the same place as the wider principles of lean manufacturing: Toyota.
The original system at Toyota used Kanban cards that each department would hand to their counterparts in order to communicate the needs of one department to another. Over time this evolved into sticky notes on a board displaying an entire project at once, which has since evolved into virtual boards. But physical cards can – and often still are – used.
In its most basic form, a Kanban board consists of three columns, each containing notes that display tasks that have been requested, are currently in progress, or have been completed
How does the Kanban system work?
Everyone has their own version of a Kanban board, but here are what you might consider the ‘basic’ ‘rules’ of using Kanban:
- The Kanban board is split into columns that track each stage of a project, e.g., Requested, In Progress, Done.
- Each project is split into individual tasks, which are placed as ‘cards’ in the Requested column. Each card represents one work item. In manufacturing, one card usually equates to one customer order.
- As customers request goods and they move into production, tasks are moved into the In Progress column, and a person’s name is usually added to the card.
- Further notes are added to communicate the current stats of the task as it develops. Screenshots, documentation and technical resources may be attached if an online Kanban system is being used. Basically, everything someone should know about a task can be included in the card.
- When the task is completed, it is moved into the Done column. The customer’s order is complete.
Kanban in lean manufacturing
Kanban is an important part of the lean manufacturing system, since it manages production through a pull system, rather than responding to predicted demand.
This is a radical shift from more traditional processes where demand is predicted in advance and materials are bought in bulk to reduce supply chain costs, such as transport.
The idea of Kanban in lean manufacturing is to cut wasted inventory by carrying only what you need in order to cover lead times, while at the same time improving communication on customer orders to ensure everyone is aware of what’s going on at all times.
Here’s a summarised version of what a Kanban operation might look like in the manufacturing context:
- Each station in your production pipeline should be treated like its own mini-business, with ‘customers’ downstream and ‘vendors’ upstream. This will make sense in a moment.
- When a customer request comes in at the bottom of the pipeline, this triggers a request for a finished product. The station nearest to the end customer (i.e. labelling) withdraws the materials it needs from their upstream ‘vendor’ (i.e. assembly), so they can perform their task and hand the product to the customer – or ship it, as would generally be the case.
- Of course, by giving the assembled product to the labelling station, that assembly station now has no goods left in its own stock. This then triggers another request to withdraw materials from the next station upstream (perhaps soldering), which then withdraws materials from the station prior, and so on and so forth back to the warehouse.
- Then, when the warehouse runs low in stock, it reorders from preferred vendors.
- So that it knows when to reorder, the warehouse may operate on what’s known as a ‘two bin’ system. Basically, the team holds all supplies and consumables in two different bins. Goods are only taken from one bin at a time, until it empties. When this happens, inventory managers know to reorder a bin’s worth of supplies from the company’s vendors.
- At this point, downstream stations start taking from the second bin (which is now the primary bin). When this empties, the original bin should be filled again.
This pipeline system is controlled by Kanban cards. The cards hold all the information that the upstream partner needs to fulfil the order for their downstream partner. When a request is made, a card is passed from one station to the next – with appropriate people notified, documents attached, and details noted.
Because everything is communicated on cards, it's all very transparent. When using a digital Kanban system, anyone can generally see what’s going on in the wider pipeline at a given moment.
Within this system, it’s key that each station only produces what it needs to meet customer demand. Typically, nothing is made if there’s no demand.
- Note: Kanban was traditionally a pull system centred around inventory, and downstream partners would pass materials withdrawal requests upstream. But these days it’s quite common for it to be used in the opposite direction – work is still only triggered by a customer request, but at that point the card may skip all the way down to the warehouse, to be passed back up as the order is completed.
By using Kanban, production is driven by actual customer orders – with each station prompting another to undertake a task when their step is completed
Advantages of a Kanban system
The main advantages of the Kanban system are that it can be used to optimise inventory, represent your workflows visually and clearly, and cut costs:
- Optimise inventory levels: In Kanban, all production is based entirely on demand. This includes the amount of stock held at a given time. This allows manufacturers to optimise their entire production process, from minimising inventory to reducing overproduction and waste.
- Visualise the workflow: With a digital Kanban especially, the entire process is represented visually – making it easier to understand and follow.
- Cut costs: When you optimise processes and ensure they are easy to follow, you theoretically reduce costs at the same time.
Challenges of a Kanban system
There can be challenges when using a kanban system, the main ones being that it can’t always cope with fluctuating demand, can be stressful to implement if done all at once, and with its need for maintenance, can become over-complicated:
- Not so good with fluctuating demand: Typical Kanban systems assume a consistent, predictable demand. If your industry is susceptible to big swings in product volumes, you may find Kanban struggles to keep up. Here, you may consider using a hybrid system of Kanban’s pull alongside analytics-based push methodologies (i.e. a heavier focus on demand forecasting and more variable inventory purchasing).
- May represent significant change: Switching to a Kanban system, and its accompanying Just-in-time inventory model, is a big change for a lot of businesses. Switching to all these elements at once can quickly lead to stress and even failure. It’s generally considered better to start small and evolve incrementally over time.
- Can get over-complicated: Kanban boards need management and maintenance, or they can grow too complex to follow. This is again where incremental evolution is important, as your company needs to build its own rules and figure out what works best for your team.
A key advantage of using a Kanban board or its digital equivalent is that project tasks – and their current status – are visible to team members at all times
8 real-world examples of companies using Kanban
To give you an idea of how Kanban is used successfully in business, here we've collected eight case studies. While many of these are large companies, the principles and practices apply to SME businesses in a range of industries.
Nike's use of Kanban
Nike is famous for having adopted a lean manufacturing approach in response to negative publicity regarding poor working conditions in its factories.
To begin this approach, the Nike leadership first walked through their own factories and surveyed people to find out how best to fix some of the notable issues. In the end, they chose to try to standardise demand in order to stabilise the work, which involved eliminating late orders and sudden changes in material. They also established Nike Grind to reduce waste, which takes recycled materials from old products and turns them into training surfaces for athletes.
Jaguar's use of Kanban to improve efficiency
People often talk about Toyota in the world of Kanban, but since its inception other automotive brands have looked into it as well. Jaguar was one of these, which had a goal to seriously reduce time to market on new product designs.
The company’s new Kanban board allowed it to make some critical changes. Notably, Jaguar was having issues with feedback on designs and design concepts, with feedback sometimes taking 12 weeks or more.
By moving to a minimum viable product concept (only giving stakeholders the information they needed to make a decision, and nothing more) and reducing batch sizes via Kanban, it cut that feedback loop from weeks to days. As Kanban turned out to be a huge success for Jaguar, design teams started making it a focal point of their daily standups.
Now Jaguar is a real leader in lean manufacturing, having cut delivery times and improved quality. It’s so successful that the team even offers other people tours of its Halewood plant to show them how to benefit from lean manufacturing principles.
Pixar's use of Kanban to 'manufacture' animation
Pixar’s co-founder and then-president Edwin Catmull initiated a Kanban approach to 3D animation that would ensure that each Pixar production was – essentially – manufactured.
By using a high-level Kanban board and lean manufacturing principles, the company was able to ensure that each team worked on its part of the film to completion before passing it down to the next team, and so on. Meanwhile, everyone could see what others were working on through the board.
Catmull mentions in his book Creativity Inc. that this manufacturing-inspired process meant that just about anyone at Pixar could stop the production line if an error was found, so it didn’t proceed further down the line and, as a result, grow more expensive to fix.
NextPhase Medical Devices' Kanban-based warehousing
NextPhase Medical Devices, previously known as Phase 2, is a manufacturer of medical technology. After implementing a number of successful business initiatives, the company found itself in a tricky position – it did not have enough warehouse space to keep up with demand.
The challenge, its leadership team decided, was to meet demand without increasing inventory space. Instead of leasing a bigger warehouse, the company focused on optimising workflows. This came in contrast, however, to the advice its team was receiving from their ERP system – which suggested that working in bigger batches was better than smaller ones.
So NextPhase sought a balance between Kanban’s continuous small-batch workflow with their ERP system’s big-batch preference. They started a series of daily standups where the team would meet with a supply chain associate who could consult on correct order placement for the work required. This helped NextPhase reduce storage requirements by 33%.
Music streaming giant Spotify is an example of how Kanban can be effective in almost any industry, with the company using this method to manage its large projects
Spotify's Kanban project planning
Even Spotify, the world’s biggest music streaming platform, uses Kanban.
The company’s Operations team was struggling to find the time to keep up with planned projects. So they turned to Kanban to split projects up into more bite-sized pieces which could be better planned for and organised.
On their board they split tasks into To Do, Doing and Done columns, and also categorise them as either tangible tasks (i.e. physical work) and intangible (i.e. planning and design). Next, they identify if tasks are small (a day’s work), medium (a few days) or large (a week), with anything that would take longer being split into smaller tasks so that they can be re-qualified as small, medium or large.
Since starting to use this system, Spotify has noticed that its lead times have become shorter and it's getting more internal tasks done, without people’s day-to-day work changing all that much.
Zara's fashion Kanban workflow
Zara – the largest fashion retailer in the world – uses Kanban at both the store and manufacturing levels, ensuring its stores can hold Just-in-time inventory levels and that it can continuously update its collections throughout the year – whereas competitors tend to update collections only four times a year.
For Zara, Kanban boards are essentially a means to connect store managers to headquarters, who are in turn connected via boards to design. Store managers ‘pull’ new stock into the pipeline by using analytics data and anecdotal evidence from customers to figure out what people want on the shelves. Commercial teams process the order and add more research, identifying what the new collection should look like so a request can be made to design.
Because Zara also utilises primarily on-shore suppliers, this means the brand can get a new product from design through to a store manager’s shop floor in just over two weeks.
Seattle Children’s Hospital: solving supply issues with Kanban
Hospitals may not immediately feel relevant to manufacturing, but the problem Seattle Children’s Hospital (SCH) faced is one that any manufacturing firm can relate to: consumables shortages were leading to staff hiding stockpiles of the items they needed on a day-to-day basis to ensure they would always have a supply. This led to a lot of problems with inventory and time wasting.
So SCH turned to the two-bin system from Kanban. Inventory managers used real-world data from a year’s worth of operations to determine what optimal stock levels looked like, then deployed the two bins. When the first bin is depleted, it can be sent to the central supply office to be scanned and reordered. Additionally, to ensure the process is transparent, staff can see the Kanban board at any time so they always know what their own supply chain looks like.
SHC found that they could reduce the size of their storage room and save money – with perishable goods no longer expiring, and staff no longer delayed by a lack of consumables.
At Seattle Children’s Hospital the Kanban two-bin system was successfully introduced to address the problem of consumables running out
Dynisco's inventory reduction using Kanban
Dynisco is a plastics extruder and manufacturer of sensors, and was having issues with its inventory carrying costs and lead times.
To tackle these, the company went through a few phases. First, it implemented a design for manufacturing and assembly best practices. This allowed it to standardise costs and simplify new product designs, a critical first step on the road to Kanban.
A manual Kanban system was next, which helped organise the flow of materials through their process and also improved client response times. However, the company was still holding too much stock.
Its third phase, therefore, was to automate their Kanban system. This started to provide Dynisco’s leaders with real-time supplier and inventory data, and it integrated easily with existing CRM and ERP systems.
With all three combined – simplification and standardisation, smooth flow of materials, fast flow of data – Dynisco was able to reduce its active inventory by 40% across all facilities.
What is Kanban software?
Kanban software facilitates the Kanban method of managing workflow using digital – rather than physical – tools. This software is based around the visual principles of the physical Kanban method, but information is displayed in an app that team members use.
Kanban software uses digital ‘cards’ for projects that are underway, so that tasks are visible to team members at all times, and backlogs of work can be cleared and work in progress minimised.
Several companies now produce Kanban software systems that help businesses control workflow by assigning tasks to team members. These are used in a range of business processes and areas – from manufacturing to marketing. Some examples are:
- Trello, which allows users to set up boards for different projects, within each of which tasks are displayed.
- Monday.com which provides Kanban-based solutions to manage a range of business activities, from software design to HR.
- Kanbanize, which provides scalable software based on the original visual Kanban concept to manage projects, including dependencies.
- Jira, a Kanban-based solution used for activities such as software development and project & product management.
Ultimately, the software product you use to manage your Kanban process will depend on the finer points of how well it’s suited to your workflows specifically, as well as other details such as cost and scalability.
Is Kanban the same as Scrum?
While Kanban and Scrum share similar ideas and are both a part of an agile workflow, the answer is: No, they are different.
Scrum operates in set blocks of time, called sprints, which are usually around two weeks in length. Each sprint is fairly regimented and led by a central Scrum leader, and changes aren’t usually made to a sprint while it’s taking place. Scrum works well when the work can be planned in detail and executed with minimal change, in order to balance both control and flexibility. Software development is an example.
Kanban involves a continuous workflow and does not operate in such fortnightly blocks, nor are there set roles within the Kanban process – although someone may ‘own’ a Kanban board in order to maintain its hygiene and offer training. This works better for companies that deliver continuously, like automotive manufacturers.
Kanban and inventory management software
Kanban is not a replacement for inventory management software, but rather one more piece of the wider puzzle. In fact, they complement each other well, given their different roles within the business. Unleashed, for example, uses a built-in Kanban view to allow the different stages of multiple production jobs to be viewed and progressed visually.
Ultimately Kanban is a controller of workflow. It helps you process goods from upstream to down, producing only what you need to meet demand and requiring only the inventory necessary to achieve that end.
Inventory management software is a controller of inventory. By utilising this type of software, you can digitise and streamline the purchasing, storing and utilising of inventory – and help improve its cost efficiency. It’ll help you manage your bills of materials, track suppliers and orders, gain visibility into costs and money pits, organise your warehouse(s), and more.
If you’ve digitised your workflow processes with a virtual Kanban board, then inventory management software is your way to modernise inventory as well, by ensuring inventory managers have real-time data and fast procurement systems to stay on top of the kanban system, for example using the two-bin method.
- Keen to find out more? Read about manufacturing inventory software
More posts like this
- Four Key Strategies to Improve Inventory Control - Companies often fail to manage inventory, or at least, don’t manage inventory effectively. Understanding the need for effective inventory management...
- How to Tackle the On-demand World of Inventory Management - It’s fast-paced, it’s busy, it’s all things go, all the time. Inventory management is an around the clock operation and the pace isn’t slowing...
- Poka-yoke in Manufacturing: Methods, Pros, Cons & Examples - Poka-yoke is a Japanese lean manufacturing strategy that aims to eliminate mistakes and defects during the manufacturing process – a simple yet effe...