
Effective inventory management start with an optimised warehouse stock control strategy. Managers must regularly inspect warehouse operations, ensuring that stock is stored in a way that allows staff to easily and safely access it.
In this article, we look at warehouse stock control: What it is, why it matters, and the best practices to implement in your facility.
What is warehouse stock control?
Warehouse stock control refers to the management and processes behind the movement of inventory within a warehouse. It concerns each step of physical order fulfilment, from receiving and putting away goods to getting them shipped out to the end customer.
Why warehouse stock control is the key to success
A properly managed warehouse is one that optimises productivity end to end and minimises the amount of time and money spent on fulfilling customer orders.
Warehouse stock control is a major contributor in pursuing these goals. By ensuring there is the right amount of parts, products, and materials available (and in the correct location), effective warehouse stock control gives businesses more opportunity to capitalise on important areas.
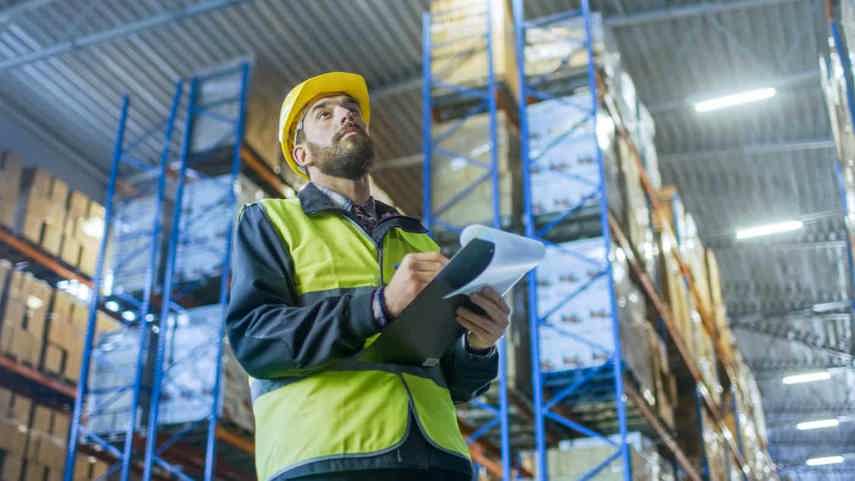
5 warehouse stock control best practices
Below are some best practice inventory control techniques to help improve your operations and ensure the smooth running of your warehouse management.
1. Have a well-organised floor plan
Effective warehouse inventory control is not simply the practice of arranging inventory stock so that it can be found quickly. While it is important for everything in the warehouse to be in its allotted place, warehouse inventory control is also about maximising productivity while saving time and money by increasing inventory accuracy.
A proven strategy for greater warehouse inventory control is to modify the floor plan for optimum efficiency. Product supply and demand changes continuously and as such you should review floorplans to adapt to season ebbs and flows. Some key areas you need to consider when planning your floor plan are:
- Making room for inwards goods receipt. Many inventory errors can occur at the receiving end when warehouse staff have insufficient space to work.
- Using clear signage and labels to direct your personnel through the warehouse, enabling them to locate inventory stock quickly and easily.
- Positioning fast moving SKUs between waist and shoulder height for rapid retrieval.
- Designating an area for damaged stock items and allocating the time for staff to deal with this stock, either daily or weekly.
Without regular maintenance, a well-organised warehouse can quickly and easily become disorganised, difficult to navigate and can slow down order fulfilment. Don’t wait for issues to arise, be proactive in managing your warehouse, use a daily checklist to ensure all areas of the warehouse are operating efficiently.
An easy and effective action you can take is to allocate time at the end of the day that allows staff to finish order processing and to clean up before clocking out. This ensures that the warehouse is organised and your inventory stock is in its rightful place ready to start afresh the following day.
2. Label everything
Clear and concise rack labels, bin labels and warehouse signage will streamline processes making it easier for staff to navigate the warehouse, and for pickers to select the right inventory stock, reducing order fulfilment errors.
Utilise labelling software to print out your product and location labels. Warehouse inventory tags, barcodes, scanners, RFID systems, automatic identification and wireless LANs provide the foundation for an efficient warehouse operation. Employees can scan freight to locations in real-time and quickly and accurately identify the precise location of inventory stock.
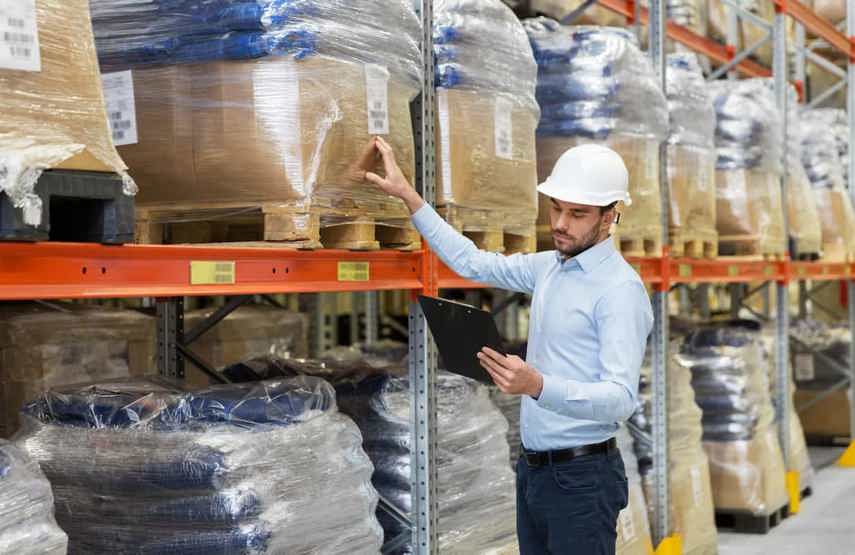
3. Know your best sellers
An advantage of optimising warehouse inventory control is that you can track sales and orders for each product or customer. This information can be extremely useful for determining what your best sellers are. By placing this high-volume stock closer to the shipping area and ensuring it is easily accessible, you can eliminate unnecessary labour time.
4. Implement cycle counts
Cycle counting is a method of perpetual inventory counting that takes place cyclically, over time with only small sections of inventory counted during each cycle. Each day, week, or month a different product is checked on a rotating schedule. There are different methods of determining which items to count and when to count them, but items of higher value should be counted more frequently.
Instead of waiting to undertake an annual physical stocktake, performing regular inventory control audits through cycle counting enables you to analyse any discrepancies to spread reconciliation throughout the year.
5. Use warehouse management software
Proper warehouse inventory control can be achieved with the right software. If you haven’t already, you should be implementing the latest software to improve your warehouse inventory control. Warehouse management tools include the use of barcode scanners, barcode labels and RFID tags to provide real-time updates and ensure quick and accurate inventory data.